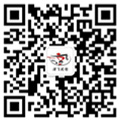
關(guān)注主辦方微信,了解更多展會信息
名稱:中國鍛壓協(xié)會
地址: 北京昌平北清路中關(guān)村生命科學園博雅C座10層
郵編:102206
電話:010- 69731006
傳真:010-53056644
郵箱:
metalform@chinaforge.org.cn
桁架機械手自動線的應(yīng)用
結(jié)合目前汽車制造業(yè)的高速發(fā)展,沖壓隨著企業(yè)用工成本上升及產(chǎn)業(yè)轉(zhuǎn)型升級的要求,單純設(shè)備性能的提高,為提高生產(chǎn)率所帶來的貢獻是非常有限的。只有制造模式和管理模式的變革,才能讓生產(chǎn)率得到飛躍式的提高。北京沖壓集自動化、柔性化和智能化于一身的制造模式將是今后制造業(yè)發(fā)展的大趨勢。 下文中提到的自動生產(chǎn)線是由高精度數(shù)控車床、高精度雙主軸數(shù)控車床、精密滾齒機、桁架自動機械手上下料、工件姿態(tài)調(diào)整裝置、物流系統(tǒng)、檢測裝置等組成。整條線的齒輪、輸入輸出軸工序內(nèi)容分為:熱處理前精車、滾齒、熱處理后精車三道工序,均采用桁架機械手進行自動上下料加工。生產(chǎn)線附加信息化生產(chǎn)管理系統(tǒng)與智能化監(jiān)控系統(tǒng),設(shè)立總控室,具有生產(chǎn)任務(wù)管理支持、質(zhì)量信息采集與分析監(jiān)控、生產(chǎn)線裝備運行狀態(tài)監(jiān)控及快速處理等功能,實現(xiàn)了設(shè)備互聯(lián)與集中控制,為創(chuàng)建數(shù)字化工廠打下了堅實的基礎(chǔ)。
圖1 桁架機器人 技術(shù)方案設(shè)計 該自動化生產(chǎn)線加工工件為汽車變速箱齒輪、輸入輸出軸。生產(chǎn)線要求兼容三種齒輪、兩種輸入軸、兩種輸出軸。設(shè)計生產(chǎn)能力為:年產(chǎn)鐵路軸承12萬套(以每班次7?h、每天3班、每月22天計算)。自動生產(chǎn)線平均無故障運行時間(MTBF)1000?h以上。3種齒輪最長加工節(jié)拍包括裝卡時間共計 130?s,4種軸最長加工節(jié)拍包括裝卡時間共計150?s。 按照自動生產(chǎn)線要求:集成精車、滾齒各工序加工,兼容三種不同規(guī)格的變速箱齒輪,四種不同規(guī)格的輸入輸出軸,同時考慮實現(xiàn)長時間無人化運轉(zhuǎn),整個生產(chǎn)線在配置車床、滾齒機的基礎(chǔ)上,增加集輸送、翻轉(zhuǎn)、抽檢一體的自動物流系統(tǒng),工件的轉(zhuǎn)序使用桁架機械手進行上下料。
圖2 變速箱齒輪自動生產(chǎn)線 根據(jù)大批量加工要求,制定如下加工工藝(圖2): 1.變速箱齒輪加工工藝流程(采用高精度雙主軸數(shù)控車床) 熱處理前工序:OP10車床1#主軸(后拉卡盤)夾持外圓——半精車內(nèi)孔、右端面——精車內(nèi)孔、右端面——OP10車床2#主軸(后拉/漲套卡盤)夾持內(nèi)孔——半精車外圓、左端面——精車外圓、左端面——OP20滾齒機夾持內(nèi)孔——精密滾齒(完成后人工轉(zhuǎn)熱處理車間)。 熱處理后工序:OP30車床1#主軸(節(jié)圓卡盤)夾持外圓——精車內(nèi)孔、右端面——OP20車床2#主軸(后拉/漲套卡盤)夾持內(nèi)孔——精車左端面。 2.變速箱輸入軸加工工藝流程(采用帶伺服尾座的高精度數(shù)控車床) 熱處理前工序:OP10車床尾座頂緊工件、主軸(后拉卡盤)夾持外圓——半精車一側(cè)外圓、端面、各檔槽——精車外圓、右端面、各檔槽——OP20車床尾座頂緊工件、主軸(后拉卡盤)夾持外圓——半精車另一側(cè)外圓、端面、各檔槽——精車另一側(cè)外圓、端面、各檔槽——精密滾齒(完成后人工轉(zhuǎn)熱處理車間)。 熱處理后工序:OP30車床主軸(后拉卡盤)夾持外圓、中心架輔助支撐——精車內(nèi)孔、右端面——OP30車床座頂緊工件、中心架松開并移動到最左側(cè)——精車各檔槽。 3.變速箱輸出軸總體加工工藝流程與輸入軸相同。 根據(jù)以上工藝路線及工廠實際情況:將變速箱齒輪的熱前半精車、熱前精車、滾齒、熱后精車四道最重要工序共兩臺高精度雙主軸數(shù)控車床及一臺精密滾齒機連線使用自動化加工。將輸入、輸出軸的熱前半精車、熱前精車、熱后精車三道最重要工序共六臺帶伺服尾座的高精度數(shù)控車床連線使用自動化加工,滾齒機對軸類零件裝卡姿態(tài)有特殊要求,暫不適合自動線生產(chǎn)。在自動化方面,齒輪自動線熱前、熱后工序采用一臺桁架機械手進行上下料,輸入軸自動線熱前、熱后工序采用兩臺桁架機械手進行上下料,輸出軸自動線形式與輸入軸自動線相同。 自動線布局 設(shè)計時需結(jié)合單臺機床加工節(jié)拍及整條生產(chǎn)線產(chǎn)能的要求,確保自動上下料時間不占用機床車削加工時間。因此,在布局上,齒輪生產(chǎn)線使用一臺桁架機械手、兩臺高精度數(shù)控車床、一臺精密滾齒機組成。同時附加料倉,完成上、下料任務(wù)。OP10車床與OP20滾齒機之間配置抽檢臺,烘干、轉(zhuǎn)序為一體的料道,實現(xiàn)零件干燥及轉(zhuǎn)序的功能。斜齒輪熱后工序上料過程中卡盤有安裝角度的要求,故熱后工序料倉與OP30車床之間配置角向定位機構(gòu),保證每次上料時零件姿態(tài)一致。 齒輪自動生產(chǎn)線采用串、并聯(lián)相結(jié)合的方式,一套機械手服務(wù)兩個工序。當產(chǎn)能飽滿時,工人在熱前、熱后工序料倉處放料,機械手從熱前工序料倉取料后先給 OP10車床上料,然后將OP10車床加工完成的工件送至轉(zhuǎn)序料道(轉(zhuǎn)序料道將工件送入滾齒機,滾齒完成的工件由工人取走轉(zhuǎn)入熱處理工序),之后從熱后工序料倉取料給OP30車床上料,再將OP30車床加工完成的工件送回熱后工序料倉。當產(chǎn)能不飽滿時,工人可只在熱前或熱后工序料倉之一處放料,機械手可只為OP10、OP30車床之一換料。 輸入(輸出)軸生產(chǎn)線使用兩臺桁架機械手和三臺高精度數(shù)控車床組成。同時附加上、下料道,形成整體化的自動化生產(chǎn)線。輸入(輸出)軸加工過程零件存在姿態(tài)轉(zhuǎn)換,OP10車床與OP20車床之間配置可使零件姿態(tài)180°翻轉(zhuǎn)的機構(gòu),保證OP20機床上料時零件姿態(tài)正確。另外,在一些生產(chǎn)節(jié)拍要求較高的場合,零件姿態(tài)翻轉(zhuǎn)機構(gòu)可以整合到機械手上,從而進一步提高自動生產(chǎn)線的工作效率。 輸入(輸出)軸自動生產(chǎn)線同樣采用串、并聯(lián)相結(jié)合的方式,兩套機械手服務(wù)三個工序。工人在熱前、熱后工序上料道處放料,并在下料道處取走加工完成品。 1#機械手從熱前工序上料道取料后先給OP10車床上料,然后將OP10車床加工完成的工件送至零件姿態(tài)翻轉(zhuǎn)機構(gòu),零件姿態(tài)翻轉(zhuǎn)完成再給OP20車床上料,并將OP20車床加工完成的工件送回熱前工序下料道。 2#機械手從熱后工序上料道取料后給OP30車床上料,然后將OP30車床加工完成的工件送回熱后工序下料道。 自動線組成 利用寧夏巨能機器人系統(tǒng)有限公司的GS050A桁架機械手、CMP06A料倉、CMR500上下料道、轉(zhuǎn)序料道、角向定位及零件姿態(tài)翻轉(zhuǎn)機構(gòu)等系統(tǒng),小巨人機床有限公司的QTN200/500、QTN200/1000、QTN200MS高精度數(shù)控車床,德國普瑞威瑪精密滾齒機組成車削滾齒自動生產(chǎn)線。完全實現(xiàn)汽車變速箱齒輪、輸入軸、輸出軸柔性生產(chǎn)制造,自動化上下料,自動沖洗以及信息化生產(chǎn)管理。 GS050A機械手,采用模塊化設(shè)計,屬于巨能公司非常成熟的系列化產(chǎn)品。根據(jù)送料要求,可附加第三個直線軸Z軸、W旋轉(zhuǎn)軸,以及其他特殊機構(gòu),相對傳統(tǒng)采用人工上下料方式,提高了數(shù)控機床的利用率。輸入(輸出)軸自動線采用常規(guī)形式的機械手上下料。斜齒輪由于采用節(jié)圓卡盤定位,常規(guī)形式的機械手無法完成上料,必須增加導(dǎo)向及彈簧推片機構(gòu),確保上料時齒輪能夠旋轉(zhuǎn)一定角度并與定位銷順暢嚙合。 車床采用小巨人機床有限公司生產(chǎn)的高精度數(shù)控車床,可根據(jù)加工工藝配置第二主軸、伺服尾座、中心架等,滿足變速箱齒輪及輸入、輸出軸精加工的需要。該設(shè)備采用MAZAK數(shù)控系統(tǒng),滿足組建數(shù)字化工廠的設(shè)備要求。 滾齒機采用德國普瑞威瑪原裝進口精密滾齒機,車床與滾齒機之間配置轉(zhuǎn)序料道。車床完成的零件只需按要求擺放至料道上即可實現(xiàn)自動化滾齒加工。滾齒加工前車床完成的零件必須非常干燥,這樣才能保證滾齒的裝及加工精度。生產(chǎn)線研制了集中輸送、清洗、烘干于一體的自動物流料道,在有效解決零件清洗干燥問題的前提下,最大程度實現(xiàn)了以盡可能小的占地面積,完成盡可能長時間的無人化自動加工。 轉(zhuǎn)序料道輸送速度1.5?m/min,應(yīng)用傳感器技術(shù),實現(xiàn)工件自動及高效清洗、烘干,提高產(chǎn)品過程質(zhì)量控制能力,并實現(xiàn)整個生產(chǎn)過程智能化控制管理。 變速箱齒輪自動線采用的CMP06A料倉結(jié)構(gòu)緊湊,可兼容直徑20~190?mm的盤類零件,與機械手配合可在一臺料倉上同時實現(xiàn)上、下料的功能,有效的降低了設(shè)備采購成本,減小了占地面積。輸入、輸出軸自動線采用的CMR500料道結(jié)構(gòu)簡單、易于維護,可兼容長度100~500?mm以內(nèi)的軸類零件,下料道還具備料滿報警功能,確保下料道零件儲存滿后及時通知工人取走。 系統(tǒng)以計算機以太網(wǎng)通訊技術(shù)、數(shù)控系統(tǒng)為基礎(chǔ),把機床工位與上層控制計算機集成連接在一起,實現(xiàn)制造企業(yè)現(xiàn)代化生產(chǎn)車間自動化網(wǎng)絡(luò)化管理。管理系統(tǒng)分為以下幾個模塊:程序傳輸管理系統(tǒng)、生產(chǎn)數(shù)據(jù)采集分析管理、車間實時可視化反饋系統(tǒng)。整個生產(chǎn)線管理系統(tǒng)通過對生產(chǎn)數(shù)據(jù)的采集和分析,從而改善生產(chǎn)設(shè)備的總體生產(chǎn)運行效率,降低生產(chǎn)成本,提高產(chǎn)品質(zhì)量。 車間可視化管理模塊中,將車間的布局按比例模擬到系統(tǒng)中,建立一個強大的電子看板,向企業(yè)用戶決策者提供真實的車間任務(wù)、人員和設(shè)備狀態(tài)信息,是有效改善企業(yè)制造過程的管理方法。 程序傳輸管模塊中,通過掃描槍掃描工單上的條形碼或者通過宏程序呼叫,服務(wù)器自動向機床發(fā)送程序,完成程序下載功能。在程序上傳方面,所有程序直接從機床上傳,服務(wù)器獲得數(shù)據(jù)后自動保存管理。 生產(chǎn)數(shù)據(jù)采集分析管理模塊中,分為機床視圖和工廠視圖兩個部分,通過數(shù)據(jù)長期采集記錄,進行系統(tǒng)數(shù)據(jù)的詳細分析,對管理者改善工廠管理提供數(shù)據(jù)支持。通過對產(chǎn)品過程質(zhì)量數(shù)據(jù)統(tǒng)計記錄,對應(yīng)各工序檢測數(shù)據(jù)對應(yīng)零件序列號,直接進入系統(tǒng)后臺數(shù)據(jù)庫,輕松實現(xiàn)對每一件產(chǎn)品的質(zhì)量追溯管理,實現(xiàn)產(chǎn)品全生命周期管理。 融合工業(yè)機器人自動化生產(chǎn)線的數(shù)字化車間,提高了加工產(chǎn)品精度和可靠性,這也必將帶動各裝備制造業(yè)的同步發(fā)展。汽車變速箱齒輪及輸入、輸出軸是汽車的重要零部件之一,必須突出可靠性與經(jīng)濟性。從某種程度上說,汽車變速箱齒輪及輸入、輸出軸制造行業(yè)對中國的汽車發(fā)展有著至關(guān)重要的作用。 由于生產(chǎn)線設(shè)備本身是高度的多功能柔性加工設(shè)備,通過對設(shè)備夾具和手爪的改變,即可以實現(xiàn)其他類型盤齒類零件、軸類零件的加工,物料輸送系統(tǒng)和計算機控制系統(tǒng)仍然保持不變,適合于批量生產(chǎn),但也可以在產(chǎn)品更換后,進行生產(chǎn)線改造和重組,模塊化的設(shè)計,方便和適應(yīng)了產(chǎn)品的變化。 智能技術(shù)和智能制造系統(tǒng)的示范應(yīng)用,沖壓行業(yè)現(xiàn)狀提高了生產(chǎn)率,優(yōu)化了要素配置,增強了企業(yè)的核心競爭力。沖壓產(chǎn)業(yè)報告利用自動化帶來的優(yōu)勢,以組建智能化制造工廠為目標,改變了傳統(tǒng)的制造生產(chǎn)模式。 來源:中國鍛壓網(wǎng) |